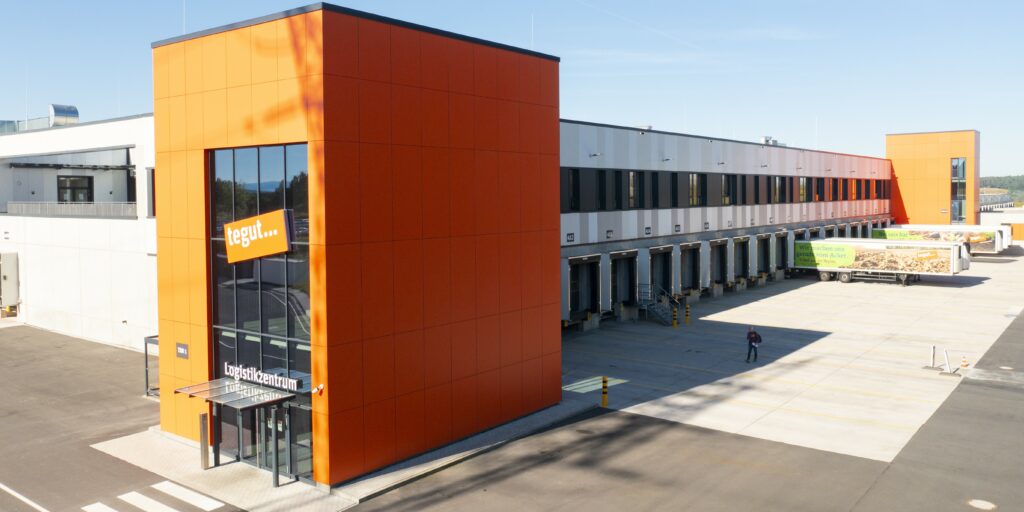
Nachhaltigkeit und Energieeffizienz im Fokus: Lebensmittelzentrallager von tegut… feierte einjähriges Jubiläum
Bildnachweis: www.aanpakringzuid.nl; Rijkswaterstaat; Combinatie Herepoort
Die Erfolgsgeschichte geht weiter: Die Mobile Fertigung der Max Bögl Wind AG hat in der Kategorie Bauverfahren den diesjährigen bauma Innovationspreis gewonnen. Das weltweit einzigartige Fertigungskonzept für hybride Windkrafttürme überzeugte die Jury als technisches und innovatives Produkt sowie für seinen Beitrag zum Klimaschutz und zur Ressourceneffizienz.
Der bauma Innovationspreis wird seit 2007 alle drei Jahre anlässlich der gleichnamigen Weltleitmesse vergeben. Mit dem jetzt ausgezeichneten mobilen Produktionskonzept ist die Fertigung von hybriden Windkrafttürmen in deutscher Werksqualität an nahezu jedem Ort der Welt möglich. Zu den Bewertungskriterien in der Kategorie Bauverfahren zählen unter anderem Innovationsgrad, Beitrag zur Ressourceneffizienz und Realisierungsanforderungen.
Mit der Mobilen Fertigung wurden bis Anfang dieses Jahres die mitunter höchsten Windkraftanlagen Südostasiens realisiert. Hier hat sich gezeigt, dass das Fertigungskonzept nicht nur technisch allen Ansprüchen deutscher Werksqualität gerecht wird, sondern zugleich auch die lokale Wertschöpfung steigert. Die Max Bögl Wind AG errichtete für den Windpark Thepharak in Huai Bong insgesamt 90 Hybridtürme mit Nabenhöhen von jeweils 156,5 m.
„Von der Idee über die Umsetzung bis hin zu dieser Auszeichnung: Das gesamte Max Bögl-Team hat mit großem Einsatz und Know-how zu diesem Erfolg beigetragen. Nur wer mutig denkt und Herausforderungen annimmt, kann innovative Projekte realisieren und nachhaltig etwas bewegen.“
Stefan Bögl
Vorstandsvorsitzender
Nach einem Jahr harter Arbeit wurde Anfang 2019 der letzte von insgesamt 90 Hybridtürmen des Pilotprojekts der Mobilen Fertigung fertiggestellt. Mit Nabenhöhen von 156,5 m zählen die Windenergieanlagen in Huai Bong zu den höchsten in Asien und zeigen damit eindrücklich die voranschreitende Entwicklung der erneuerbaren Energien in Thailand. Um höchste Effizienz im Prozessablauf zu gewährleisten, erfolgte parallel zur mechanischen Turmmontage eine eng getaktete Installation der Anlagen und Rotorblätter durch den Kunden, die Anfang Februar abgeschlossen war. Bereits Ende März konnten die Windkraftanlagen in Betrieb gehen und an das regionale Stromnetz angeschlossen werden.
„Dass alles so reibungslos geklappt hat, lag nicht nur an Technik und Material. Zum Erfolg des Projekts hat maßgeblich das zwischenmenschliche Verhältnis von unseren Mitarbeitern und den thailändischen Kollegen beigetragen.“
Udo Hiller
Zentralbereichsleiter Windkraftanlagen, Projektleiter Thailand
Der Standort in Thailand fernab der Heimat stellte für das Projektteam eine besondere Herausforderung dar. Neben dem richtigen Umgang mit den klimatischen Bedingungen war es von großer Bedeutung, den rund 150 lokalen Mitarbeitern die Abläufe der Arbeitsprozesse sowie das relevante Know-how zu vermitteln, um den Qualitätsstandard „Made in Germany“ zu gewährleisten. Durch die Zusammenarbeit mit Menschen aus einer anderen Kultur konnten die Mitarbeiter vor Ort viel lernen. Auch die Angestellten aus Deutschland hatten die Möglichkeit, neue Erfahrungen zu sammeln. Mit dem erfolgreichen Projektabschluss beweisen die Mitarbeiter der Max Bögl Wind AG, dass der innovative Ansatz der Mobilen Fertigung zukunftsweisend ist und dazu beitragen kann, internationale Klimaziele voranzutreiben.
Weitere Informationen zum Leistungsbereich Erneuerbare Energien finden Sie auf unserer Website:
Bildnachweis: www.aanpakringzuid.nl; Rijkswaterstaat; Combinatie Herepoort
Der Ringweg Groningen ist eine Verkehrsader, die die Provinz-Hauptstadt Groningen umgibt und die niederländischen Autobahnen A7 und A8 sowie die umliegenden Gebiete und das Zentrum von Groningen miteinander verbindet. Seine Funktion als bedeutender Verkehrsknotenpunkt in Kombination mit dem stetigen Wachstum der beliebten Universitäts-Stadt führten im Laufe der Jahrzehnte zu immer stärkeren Belastungen der Infrastruktur. Aus diesem Grund wurde beschlossen, den südlichen Ringweg grundlegend zu erneuern.
Mit rund 100.000 Fahrzeugen auf der A60 und ca. 80.000 Fahrzeugen pro Tag auf der A63 ist das Autobahnkreuz Mainz-Süd ein hoch frequentierter Verkehrsknotenpunkt, an dem wichtige Verkehrsströme des Rhein-Main-Gebiets zusammenlaufen. Eine Prüfung der beiden Kreuzungsbauwerke hat ergeben, dass die beiden bestehenden Brücken dem hohen Verkehrsaufkommen nicht mehr gewachsen sind und ein Ersatzneubau erforderlich ist.