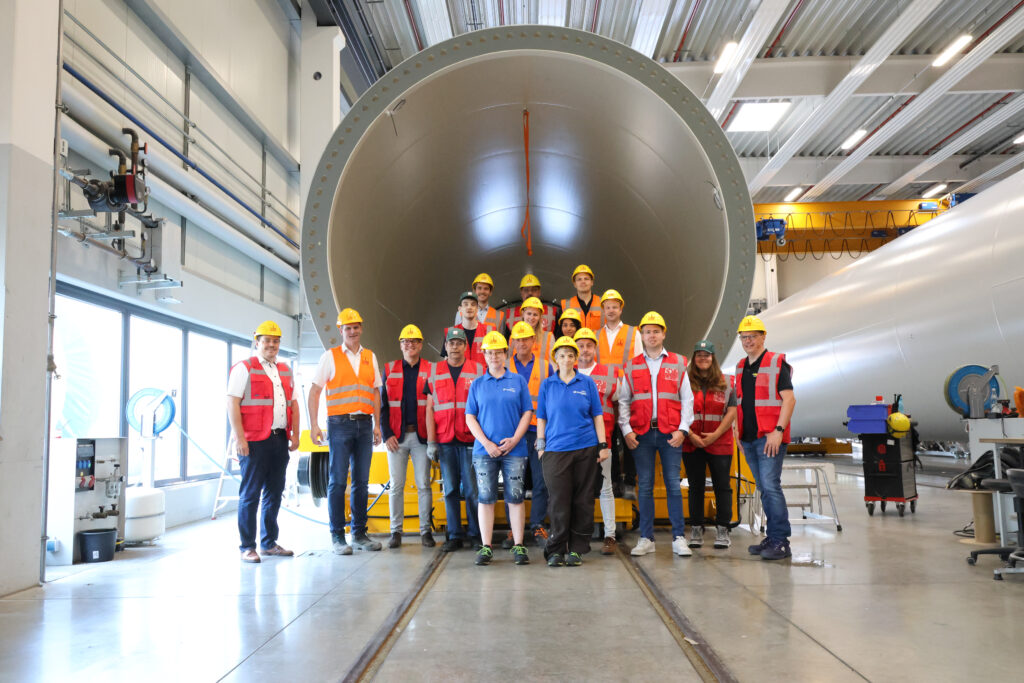
Gelebte Inklusion: Firmengruppe Max Bögl kooperiert mit Regens Wagner und den Jura Werkstätten
Bildnachweis: www.aanpakringzuid.nl; Rijkswaterstaat; Combinatie Herepoort
Z
ur Reinhaltung der Isar führt Max Bögl derzeit im Auftrag der Münchner Stadtentwässerung eine Sanierung des Kanalnetzes in der Montgelasstraße durch. Notwendig ist die Baumaßnahme, da starke Regenfälle zu einer Überlastung der Mischwasserkanalisation rechts der Isar führen können und das überschüssige Regen- und Schmutzwasser zur Entlastung in den Fluss abgeleitet werden muss. Um das zukünftig zu minimieren, wird mittels eines Dükerbauwerks und eines Mischwasserkanals DN 1600 eine Verbindung mit dem Klärwerk links der Isar geschaffen, das über die nötigen hydraulischen Kapazitäten verfügt.
Um bei der Startbaugrube Tiefe einzusparen, verläuft der Dükervortrieb anfangs steil nach unten und geht dann in einem vertikalen Bogen in ein geringes Gefälle unter der Isar über. Aufgrund des relativ engen Ausrundungsradius des Bogens wurden zur Druckübertragung der Vortriebsrohre DN 1600 bereits in der Ausschreibung hydraulische Fugen vorgesehen. Für die Ausführung wählte Max Bögl das System der Firma Jackcontrol. Diese hydraulischen Fugen sorgen zum einen für eine günstige Spannungsverteilung in der Rohrverbindung und ermöglichen damit höhere zulässige Vortriebskräfte.
Zum anderen überwachen und dokumentieren an den Rohren angebrachte Sensoren auch die Belastungen während des Vortriebs und gewährleisten somit eine umfängliche Qualitätssicherung. Diese Möglichkeit der Überwachung und Ermittlung der maximalen Vortriebskräfte bot das bestehende System schon seit Langem. Mit der neuen Software MSS sollen jedoch zukünftig Digitalisierungspotenziale noch besser genutzt und ausgeschöpft werden. Dazu werden alle für den Vortrieb und den fertigen Rohrstrang relevanten Informationen und Daten in einer cloudbasierten Datenbank gesammelt und gespeichert, um daraus neue Anwendungen für Vortriebsunternehmen und berechtigte Dritte zu kreieren.
Voraussetzung für die Nutzung von MSS ist die netzwerkbasierte Plattform MT.connect. Diese Hardware reduziert die im Tunnel zu installierenden Systemkomponenten auf ein Minimum und ermöglicht dank WLAN neue Kommunikationswege zwischen Tunnel und Oberfläche. Auf der Baustelle in München wurden neben Vermessungs- und Überwachungsdaten aus der hydraulischen Fuge auch die Daten von der Vortriebsmaschine und vom automatischen Bentonit-Schmiersystem (Design und Bau ebenfalls von Max Bögl) über elektronische Schnittstellen in das MSS eingespeist.
Relevante Daten aus dem Baugrundgutachten und weitere baustellenspezifische Informationen waren ebenfalls in das System eingepflegt. Auf dem Rechner können dann alle Daten präzise analysiert, ausgewertet und in anschaulichen 3D-Grafiken visualisiert werden. Auf diese Weise lassen sich auch Arbeitsberichte (pro Schicht, Tag oder Woche) zur optimalen Dokumentation der Baustellen generieren und grafisch darstellen.
Aufgrund der guten Erfahrungen mit MSS im Zuge des Münchner Kanalsanierungsprojektes hat sich die Firmengruppe Max Bögl dazu entschieden, in eigene Hardwarekomponenten in diesem Bereich zu investieren, um den laufenden Prozess der Digitalisierung weiter voranzutreiben und bei zukünftigen Projekten weiterzuentwickeln.
Für Matthias Ullmann, Abteilungsleiter für den Bereich Rohrvortrieb bei Max Bögl, hat sich der Einsatz des Microtunneling Support Systems auf der Baustelle bestens bewährt. Gegenüber „mbquadrat“ äußert er sich zu den Vorteilen und zukünftigen Einsatzmöglichkeiten.
Wie waren Ihre Erfahrungen mit dem System MSS im ersten „echten“ Baustelleneinsatz?
Matthias Ullmann: Die Oberfläche ist benutzer- und bedienerfreundlich und die Software hat im Baustellenbetrieb gut funktioniert. Die Erfassung, den Transport und die Auswertung der Daten in einem System zu bündeln, sorgt für eine deutliche Vereinfachung und für eine größere Transparenz des Vortriebsgeschehens. Das bringt uns von der Installation der Instrumente über deren Verkabelung bis hin zur Speicherung und Auswertung erhebliche Vorteile.
Verbesserte Dokumentation und vereinfachter Informationstransfer:
Welche Vorteile ergeben sich daraus dem Kunden gegenüber und innerhalb des Projektteams?
Matthias Ullmann: Bei komplexen Bauaufgaben wird es immer wichtiger, dass Informationen möglichst einfach und schnell allen Projektbeteiligten zur Verfügung stehen. Durch derart digitale Lösungen können alle Beteiligten von überall her auf das System zugreifen – und damit auf alle relevanten Parameter der Baustelle. So können wir beispielsweise jederzeit einen Soll-Ist-Vergleich des Vortriebs durchführen und falls nötig reagieren.
Wie sehen Sie die zukünftigen Möglichkeiten von MSS bei komplexen Planungs- und Bauprozessen im Bereich Building Information Modeling (BIM)?
Matthias Ullmann: Für uns ist das Microtunneling Support System mit den erfassten und gespeicherten Daten ein Baustein, um eine Vortriebsbaustelle BIM-tauglich zu machen. Ziel von Max Bögl ist es, mit digitalisierten Prozessen und derart technischen Möglichkeiten den Rohrstrang als eigentliches Bauwerk zu dokumentieren und digital abzubilden. Die Programmierung dazu soll noch in diesem Jahr abgeschlossen werden. Dann sei man in der Lage, am Ende des Projektes dem Bauherrn einen Datenträger übergeben zu können, auf dem er in einem BIM-kompatiblen Format alles Wissen über sein Bauwerk bekommt.
Weitere Informationen zum Leistungsbereich Infrastruktur finden Sie auf unserer Website:
Bildnachweis: www.aanpakringzuid.nl; Rijkswaterstaat; Combinatie Herepoort
Bildnachweis: www.aanpakringzuid.nl; Rijkswaterstaat; Combinatie Herepoort
Der Ringweg Groningen ist eine Verkehrsader, die die Provinz-Hauptstadt Groningen umgibt und die niederländischen Autobahnen A7 und A8 sowie die umliegenden Gebiete und das Zentrum von Groningen miteinander verbindet. Seine Funktion als bedeutender Verkehrsknotenpunkt in Kombination mit dem stetigen Wachstum der beliebten Universitäts-Stadt führten im Laufe der Jahrzehnte zu immer stärkeren Belastungen der Infrastruktur. Aus diesem Grund wurde beschlossen, den südlichen Ringweg grundlegend zu erneuern.