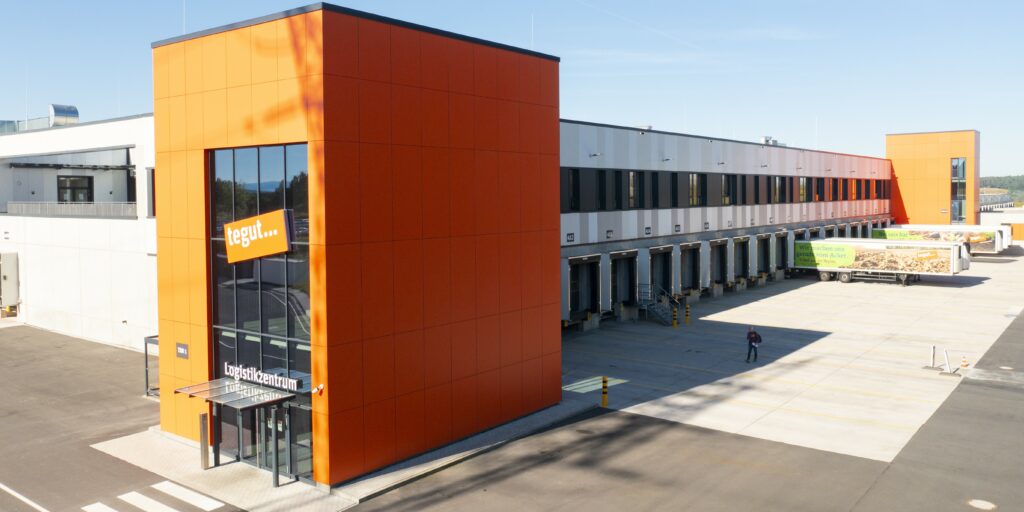
Nachhaltigkeit und Energieeffizienz im Fokus: Lebensmittelzentrallager von tegut… feierte einjähriges Jubiläum
Bildnachweis: www.aanpakringzuid.nl; Rijkswaterstaat; Combinatie Herepoort
Zur Verbesserung des Verkehrsflusses auf der A6 zwischen Nürnberg und der Landesgrenze zu Baden-Württemberg wird die Autobahn dreispurig ausgebaut. Dazu ist es notwendig, die Brückenbauwerke der beiden Richtungsfahrbahnen an der Anschlussstelle Ansbach über die B13 an die neue Fahrbahnbreite anzupassen. Die Firmengruppe Max Bögl wurde von der Autobahn GmbH mit dem Abbruch der Bestandsbrücken und deren Neubau beauftragt.
Bei einem Verbundträger Bögl handelt es sich um ein Fertigteil, das aus einem stählernen Längsträger und einem Flansch aus Beton besteht. Sowohl die Stahl- als auch die Betonkonstruktion werden im eigenen Stahlbau und Fertigteilwerk hergestellt.
Mit einer Länge von rund 55 m und einer Bauteilhöhe von 3,25 m sind die Träger für das Projekt bei Ansbach die größten Verbundträger Bögl, die jemals im Werk gefertigt worden sind. Die enorme Größe und ein maximales Einzelgewicht von 114 t machen die Handhabung der Träger bei der Herstellung, der Auslieferung und der Montage zu einer besonderen Herausforderung.
Innerhalb eines Zeitraumes von 10 Monaten wurden die Träger projektiert und hergestellt, bevor sie auf die Baustelle transportiert und vor Ort montiert werden konnten. Die Projektierung der Träger erfolgte in ständiger Abstimmung aller involvierten Abteilungen – dazu zählten u. a. das Technische Büro Bögl, die Stahlbaufertigung, das Fertigteilwerk, Transport und Geräte und die Baustelle.
Aufgrund des bereits erprobten Produktionsablaufes bei der Fertigung der Stahlkonstruktion konnten auch die Träger für das Ansbach-Projekt trotz ihrer außergewöhnlichen Abmessungen schnell und mängelfrei hergestellt werden. Die Herstellung des Betonflansches erfolgte in einer auf alle Trägerquerschnitte und -längen konfektionierten Standardschalung.
Für den Einhub der Träger wurden die Unterbauten – Fundamente und Widerlager – vorab hergestellt. Anschließend wurden die Träger auf jeweils zwei Auflagerstühlchen pro Achse abgesetzt. Diese Stühlchen wurden im Vorfeld genauestens eingemessen, ausgerichtet und dann ins Widerlager eingebunden.
Nach der Fertigung der Träger und den vorbereitenden Maßnahmen auf der Baustelle wurden die Verbundträger mittels zweier Travellifts verladen. Die gesamte Transportlänge von 65 m, eine gesamte Transporthöhe von 4,48 m und ein Gesamtgewicht der Fahrzeugkombination von 190 t waren eine besondere Herausforderung bei der Anlieferung der Träger.
Um die Transporthöhe einhalten zu können, wurden die Fahrzeuge abgesenkt. Zudem wurde die Strecke – von unserem Fertigteilwerk in Sengenthal bis zur Baustelle in Ansbach – bereits im Vorfeld bis ins kleinste Detail begutachtet, wobei die kritischen Stellen genau vermessen worden sind. Die Schleppkurven der Fahrzeuge mit den Trägern wurden durch ein entsprechendes Programm vorher simuliert und virtuell abgefahren. Bei einer genehmigten Transporthöhe von max. 4,51 m waren im Gesamttransportsystem nur 3 cm Spielraum nach oben, um Ungenauigkeiten auszugleichen.
Am 16.07.2022 kamen die ersten Träger um 20:00 Uhr auf die Baustelle. Der daran anschließende Einhub erfolgte mittels zweier 450-Tonnen-Autokrane im Tandemhub. Eine der größten Herausforderungen des Einhubs war es, die Träger trotz der beengten Platzverhältnisse – bedingt durch die beiden Kranaufstandsflächen, die bereits montierten Träger und die befahrene Bestandsbrücke – lagegenau einzufädeln. Nach Ablegen eines jeden Trägers wurden diese gegen Kippen abgesichert. Mit diesem Vorgehen wurden die insgesamt sieben Verbundträger Bögl der Reihe nach montiert.
Durch diese Bauweise, bei der die werksgefertigten Fertigteile ohne Mittelpfeiler von Widerlager zu Widerlager gespannt werden, konnten die Beeinträchtigungen des Verkehrs auf ein Minimum reduziert werden. Im Sommer 2023 wird dann der zweite Bauabschnitt realisiert.
Weitere Informationen zum Leistungsbereich Infrastruktur finden Sie auf unserer Website:
Bildnachweis: www.aanpakringzuid.nl; Rijkswaterstaat; Combinatie Herepoort
Der Ringweg Groningen ist eine Verkehrsader, die die Provinz-Hauptstadt Groningen umgibt und die niederländischen Autobahnen A7 und A8 sowie die umliegenden Gebiete und das Zentrum von Groningen miteinander verbindet. Seine Funktion als bedeutender Verkehrsknotenpunkt in Kombination mit dem stetigen Wachstum der beliebten Universitäts-Stadt führten im Laufe der Jahrzehnte zu immer stärkeren Belastungen der Infrastruktur. Aus diesem Grund wurde beschlossen, den südlichen Ringweg grundlegend zu erneuern.
Mit rund 100.000 Fahrzeugen auf der A60 und ca. 80.000 Fahrzeugen pro Tag auf der A63 ist das Autobahnkreuz Mainz-Süd ein hoch frequentierter Verkehrsknotenpunkt, an dem wichtige Verkehrsströme des Rhein-Main-Gebiets zusammenlaufen. Eine Prüfung der beiden Kreuzungsbauwerke hat ergeben, dass die beiden bestehenden Brücken dem hohen Verkehrsaufkommen nicht mehr gewachsen sind und ein Ersatzneubau erforderlich ist.